Digital Twins and the Industrial Revolution
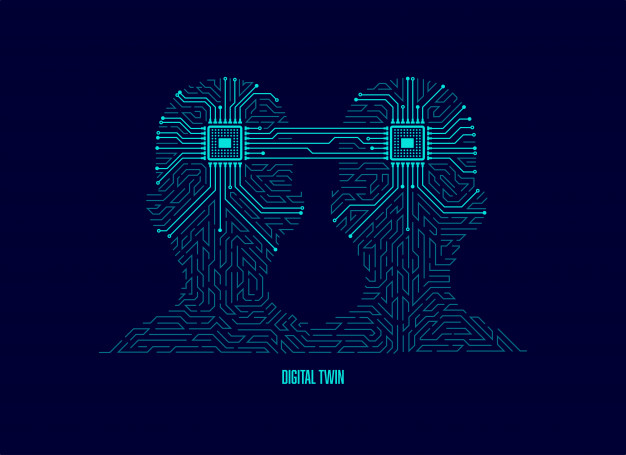
October 5, 2020
Digital twins are capturing the spotlight beyond creating information modeling, they evolve rapidly, and enable asset-centric organizations to converge their engineering, operational, and information technologies for immersive visualization and analytics visibility.
A digital twin refers to virtual replicas of products, services, or systems that are used to prevent problems and facilitate experimentation. Digital twins integrate exponential technologies such as the Internet of Things, Artificial Intelligence, machine learning, and software analytics to create digital simulation models that update and change as their physical counterparts change, these twins replicate through Cyberphysical Systems (CPS). Consequently, we have a system that automatically learns how a real system works, with automatons, robots, people, vehicles, objects, products, etc.
But with the advent of the Internet of Things (IoT), sensors, big data, and cloud computing, they can now create digital twins of anything displayed and behaved in a variety of different scenarios. In this way, machine learning and artificial intelligence algorithms can be applied to them to help them operate more efficiently.
Components of a digital twin
- Digital Simulation: a model that defines the system.
- Intelligent automation and sensors connected to the Internet of Things (IoT): for the interrelationship between the real system and the model through IoT devices.
- Artificial intelligence analytics: layer to exploit the data generated by the model.
- Virtual reality and augmented reality (VR/AR).
- Computer-aided 3D design.
Classification of digital twins
Equation-based: a digital twin whose development is model-based and uses equations to describe the behavior of industrial systems.
Data-based: system behavior is barely observed during the engineering phase, during the production process, these, which allow the creation of a digital twin from this data.
Hybrid: it is often impossible to simulate all the physical behavior of a system in real time, so reduced models should be used.
Uses of digital twins
Application scenarios for digital twins include:
- Check if a product meets the specifications devised in its design before making a real prototype or entering production.
- Identify whether a product is stable and intuitive without having to perform costly laboratory tests or large-scale tests.
- Monitor potential product failures based on many more simulations than we could get in a traditional environment.
- Detect inefficiencies or areas of improvement in the manufacturing processes of an industrial plant.
- Improve the preventive maintenance of the machinery used and test different production models without having to implement them in the daily operation, reducing the risks associated with these changes.
- Reduce factory downtime and optimize power consumption.
- Create a single point of visualization of data from factories, centralizing the big data of the company, reducing management costs and providing better variables to managers when managing the business.
What does a digital twin bring?
A digital twin focused on the industrial field allows having a virtual model of a plant that the user can access without being in person there. To do this, the model is presented by means of a VR display device, achieving a 100% immersive experience. Once represented, it is possible to present information associated with each virtual item. This is especially interesting when combined with data sources such as IoT sensors or signals from control systems; the ability to model different locations allows information to be centralized and available contextually, in real time.
Enabling an open environment while improving security for Digital Twins
Cloud technology is crucial for digital twins by enabling collaboration, improving decision-making, and delivering better project and asset outcomes with better performance. To have open, live access to digital engineering model information, organizations must implement a connected data environment. This type of environment allows you to combine engineering technologies with information technologies and operational technologies to improve the performance, safety and reliability of your production assets.
A look at the benefits
The digital twin of a product is created from the definition and design stage of a planned product. This allows engineers to simulate and validate product properties depending on the respective requirements: for example, is the product stable and intuitive to use? Does the car body offer as little air resistance as possible? Does electronics work reliably? Whether itβs mechanics, electronics, software, or system performance, the digital twin can be used to test and optimize all of these elements in advance.
When a company builds a digital replica of its products, the environments in which it operates, and the systems that produce them, it can predict virtually everything that will happen in the physical world. For engineers, digital twins are very useful because, with a detailed history of the previous model, they can fix errors and create new, more reliable versions.
In turn, the digital performance twin constantly receives operational data from the products or the production plant. This allows information, such as machine health data and power consumption data from manufacturing systems, to be constantly monitored. At the same time, this makes it possible to perform predictive maintenance to avoid downtime and optimize power consumption.
Thanks to better documentation of manufacturing processes and production parameters, the potential offered by the digital twin in the area of quality management is just as exciting. If manufacturers know exactly which component has been installed, with what features, which products and how it was installed, they can provide a specific response to potential problems and optimize their processes.
The interoperability of digital twins with other applications is another major advantage. Digital twins open up new opportunities for all kinds of new services. Due to the rapid increase in the adoption of reality modeling, start-ups are replacing traditional inspection and control organizations, generating digital asset models rather than reports.